November 2024 Health & Safety Newsletter
- matthewbarker47
- Nov 27, 2024
- 9 min read
Updated: Nov 29, 2024
Health & Safety Statistics 23/24
The Health & Safety Executive (HSE) recently released their annual statistics on accident and injury health figures in Great Britain relating to 2023/2024, examples are listed below:

The most common work-related non-fatal injury was slips, trips or falls on the same level, accounting for 31% of total accidents. Accidents caused by moving objects and falls from height appear to have dropped, accounting for 10% and 8% of workplace incidents, respectively.
Work-related Ill Health
All Illness
In 2023/24, an estimated 1.7 million workers in Great Britain were suffering from an illness which they believed was caused or made worse by work (either new or long standing), equivalent to a rate of 4,940 per 100,000 workers (4.9%).
The rate of self-reported work-related ill health had been falling in earlier years but in the recent years prior to the coronavirus pandemic had been broadly flat. The current rate is higher than the 2018/19 pre-coronavirus level.
Figure 1: Estimated rate of self-reported work-related ill health per 100,000 workers, Great Britain (new and long-standing cases). Source: Labour Force Survey
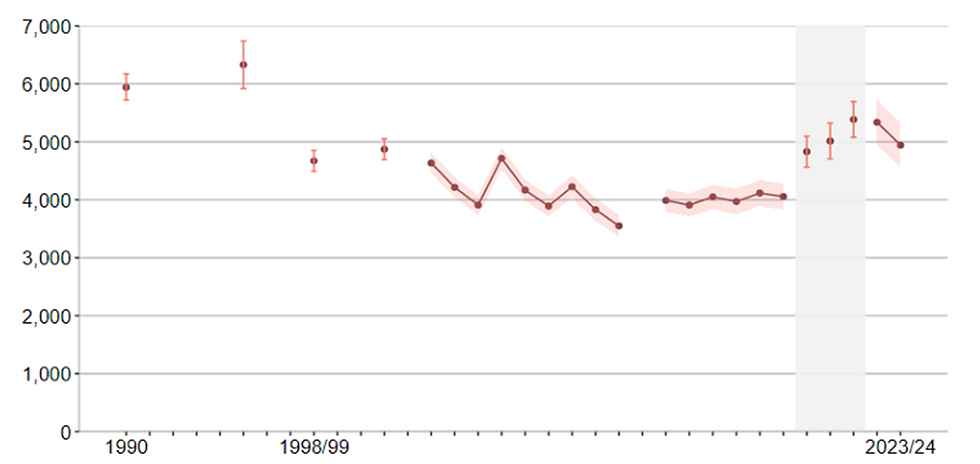
Chart notes:
• Ill health data was collected periodically up until 2003/04 and annually thereafter except for 2012/13 where no data was collected. • Estimates for 1998/99 and earlier relate to England and Wales; thereafter estimates relate to GB. However, rate estimates for England and Wales and GB are broadly comparable.
• Shaded area around line and error bars around points represents a 95% confidence interval.
• Data for 2019/20 to 2021/22 includes the effects of the coronavirus pandemic, shown inside the shaded grey column.
Musculoskeletal Disorders
Musculoskeletal disorders accounted for around a third of all cases of self-reported work-related ill health to workers in Great Britain in 2023/24.
Prior to the coronavirus pandemic, the rate of self-reported work-related musculoskeletal disorders showed a downward trend. The current rate, at 1,600 cases per 100,000 workers (1.6%), is similar to the 2018/19 pre-coronavirus level.
Figure 2: Estimated rate of self-reported work-related musculoskeletal disorders per 100,000 workers, Great Britain (new and
long-standing cases).
Source: Labour Force Survey

Chart notes:
• Ill health data was collected periodically up until 2003/04 and annually thereafter except for 2012/13 where no data was collected.
• Estimates for 1998/99 and earlier relate to England and Wales; thereafter estimates relate to GB. However, rate estimates for England and Wales and GB are broadly comparable.
• Shaded area around line and error bars around points represents a 95% confidence interval.
• Data for 2019/20 to 2021/22 includes the effects of the coronavirus pandemic, shown inside the shaded grey column.
Stress, depression or anxiety
Stress, depression or anxiety accounted for around a half of all cases of self-reported work-related ill health to workers in Great Britain in 2023/24.
In the recent years prior to the coronavirus pandemic, the rate of self-reported work-related stress, depression or anxiety had shown signs of increasing, having been broadly flat since 1998/99. The current rate, at 2,290 cases per 100,000 workers (2.3%), is higher than the 2018/19 pre-coronavirus level.
It is likely that awareness of work-related stress and attitudes towards it changed in the 1990s, which will have affected reporting levels.
Figure 3: Estimated rate of self-reported work-related stress, depression or anxiety per 100,000 workers, Great Britain (new and long-standing cases).
Source: Labour Force Survey

Protecting Young People at Work
Workers are as likely to have an accident in the first 6 months at a workplace as they are during the whole of the rest of their working life.
Young people are especially at risk as they are likely to be new to the workplace and less aware of risks.
When you employ young people under the age of 18, you have the same responsibilities for their health, safety and welfare as you do for other workers. This applies whether they are:
a worker
on work experience
an apprentice
Risks to young people
Young people are likely to be new to the workplace and so are at more risk of injury in the first six months of a job, as they may be less aware of risks. They will often be vulnerable, as they may:
lack experience or maturity
not have reached physical maturity and lack strength
be eager to impress or please people they work with
be unaware of how to raise concerns
Training and supervision
Young people need clear and sufficient instruction, training and supervision so they understand the importance of health and safety and can work without putting themselves and other people at risk. They may need more supervision than adults.
Work experience
Work experience and work-based learning will be the first time most young people experience the work environment.
Good preparation and organisation of placements is essential if these opportunities are to be helpful and safe introductions to work.
Greatest risks to young people
For many young people the workplace will be a new environment and they will be unfamiliar with 'obvious' risks and the behaviour expected of them.
They may lack experience or maturity. Make sure they understand what is expected of them, check they understand and can remember and follow instructions.
When assessing a young person's physical capability, you could simply ask yourself if a still developing young person could lift the weights older, more experienced workers can.
Levels of risk
Low risk environments
For placements in low-risk environments, such as offices or shops, with everyday risks that will mostly be familiar to the young person or student, your existing arrangements for other workers should be enough.
Less familiar risks
For environments with risks less familiar to them (for example in light assembly or packing facilities), you should plan to manage the risks. This should include induction, supervision, site familiarisation, and any protective equipment needed.
High-risk environments
For work in a higher-risk environment such as construction, agriculture and manufacturing:
consider the work they will be doing or observing, the risks involved and how they are managed
satisfy yourself that the instruction, training and supervisory arrangements have been properly thought through and work in practice
Case Studies
Manchester Engineering Firm Fined After Apprentice Loses Fingers
A Manchester-based engineering company has been fined £500,000 after a young apprentice lost the use of two fingers when using a horizontal bandsaw.
The apprentice, who was just 18 at the time, suffered the serious injuries to his fingers in an incident in Worsely, on 7 November 2022. While one finger was severed completely, the other was surgically re-attached. However, the now 20-year-old has been left with very little movement and nerve damage in that finger. He had only been on a placement with the firm in order to gain experience in fabrication and engineering and was just over a month into this placement when the incident occurred.
An investigation by the Health and Safety Executive (HSE) found that he was being taught how to weld as part of his apprenticeship placement. After a brief period of verbal training, he was permitted to cut lengths of steel into these sections using a horizontal bandsaw, which was located in a shipping container some distance away from the main workshop.
He had been working unsupervised when he noticed the bandsaw was not completing a full cut due to a build-up of metal debris underneath the sawblade. As he attempted to clear away the debris, his fingers came in contact with the moving sawblade, instantly severing one finger and severely damaging another. He was taken to hospital where he remained for six days.
The investigation also found that the company had failed to carry out a suitable and sufficient risk assessment, resulting in a failure to provide suitable guarding arrangements on the bandsaw and had failed to put in place an adequate safe system of work. It also revealed inconsistencies and inadequacies in the provision of information, instruction, training and supervision for those required to use the bandsaw.
The company pleaded guilty to breaching Section 2(1) of the Health and Safety at Work etc. Act 1974 at Manchester Magistrates’ Court. They were fined £500,000 and ordered to pay £5,317 costs at a hearing at on 6 November 2024.
Court Upholds a Supermarket Conviction After Adjustments Not Made for Vulnerable Worker
In 2014, Matthew Gunn died aged 27 following a fall on a staircase at his place of work, a Tewkesbury branch of the supermarket chain .
Matthew had epilepsy, which could cause him to collapse without warning. He had worked for Morrisons for close to a decade, therefore his employers were aware of his condition and had previously made adjustments to ensure Matthew had a safe working environment.
The company required employees to deposit their personal items in lockers located up a flight of stairs at the start of each shift. In June 2014, a formal occupational health assessment endorsed a recommendation that Matthew’s possessions locker be moved to the ground floor to avoid the risk to Matthew’s safety of a collapse on the stairs.
Matthew’s colleagues reported previous occasions where colleagues had found him having a seizure on the stairs and had expressed concerns about Matthew’s safety.
Tragically, the recommendation to move Matthew’s locker was not implemented, and in September 2014, Matthew experienced a seizure in the stairwell, fell, and sustained serious head injuries. Matthew died in October 2014, having never recovered from the fall.
In February 2023, the supermarket was convicted of:
Failing to ensure, so far as reasonably practicable, the health and safety of employees, contrary to s.2 of the Health and Safety at Work Act 1974.
Failing to carry out a suitable and sufficient assessment of the risks to the health and safety of employees, contrary to the Management of Health and Safety at Work Regulations 1999 (the “MHSWR“).
Failing to review any assessment of the risks to the health and safety of employees, contrary to the MHSWR.
The offences were placed in the highest category of culpability and harm and the supermarket was fined £3.5m.
Food Manufacturer Owner Fined £1.28m After Employee Crushed to Death by Lorry
The owner of a well known food manufacturer has been fined £1.28 million after an employee was killed by a lorry that was delivering supplies to the bakery where it makes its pasties.
Paul Clarke was fatally crushed on 2 December 2021 after being struck by the vehicle as it reversed into a loading bay at The Cornwall Bakery, Callington. He worked as an intake operator at the bakery, had been moving strip curtains in the loading bay before being struck by the lorry.
A Health and Safety Executive (HSE) investigation found the company had not assessed the risks associated with the temporarily installed strip curtains and that there was no safe system of work to move them out of the way when the lorries reversed into the loading bay. The strip curtains had been installed in place of a faulty roller door.
The site staff had not been provided with training or instructions to move the curtains and had devised their own methods, which included standing in the yard behind reversing vehicles. Mr Clarke was new to the role and was working his first lone shift. Management failings had not picked up the additional risks associated with this task.
The company, of Melton Mowbray, Leicestershire, pleaded guilty to breaching Section 2(1) of the Health and Safety at Work etc. Act 1974. The company was fined £1.28 million and ordered to pay £24,106 in costs at Plymouth Magistrates’ Court on 7 November 2024.
HSE inspector Aimie Baker said: “Workplace transport incidents involving pedestrians are a major cause of fatal injuries in the workplace with 25 such recorded fatalities in 2023/24. Employers should plan their workplace to reduce contact between pedestrians and vehicles.
“Their risk assessment should consider workplace transport activities, including loading and unloading, and ensure that pedestrians are safe from the risks associated with vehicle movements where they interact. The management arrangements further require employers to monitor and review their measures as appropriate for the risks.”
Indoor Workplaces
Indoor temperatures are far easier to control, but safety is still of concern. Employers should provide:
A reasonable working temperature in workrooms;
Local heating or cooling (using fans, opening windows; using radiators) where a comfortable temperature cannot be maintained throughout each workroom, such as in hot and cold manufacturing processes;
Rest facilities where necessary e.g. for hot work or warm clothing in cold stores;
Heating systems which do not give off dangerous or offensive levels of fume into the workplace.
Outdoor Workplaces
When working outdoors, the weather can have a serious impact on worker’s health if the risks have not been properly managed.
This impact may be immediate or occur over a longer time, leading to conditions like skin cancer. The weather can also affect a worker’s ability to keep safe, for example when handling machinery.
There are simple actions you can take to protect people working outdoors.
Ensure the personal protective equipment issued is appropriate;
Provide mobile facilities for warming up, and soup or hot drinks;
Introduce more frequent rest breaks;
Consider delaying the work until warmer times of the year without compromising on safety;
Make sure workers can recognise the early symptoms of cold stress, such as a cough or body aches.
Comments